Truck collision repairs are more than skin deep in the era of ADAS
Advanced driver assistance systems (ADAS) are designed to prevent or minimize truck collisions, but they can also introduce new challenges for repair facilities looking to fix any damage that does occur.
Look no further than a seemingly simple windshield repair. Choosing a thicker double-sided tape to reattach a forward-facing camera can affect how the lens will focus, says Chris Sterwerf, COO of Fairfield Auto and Truck Service. The choice of glass can make a difference as well.
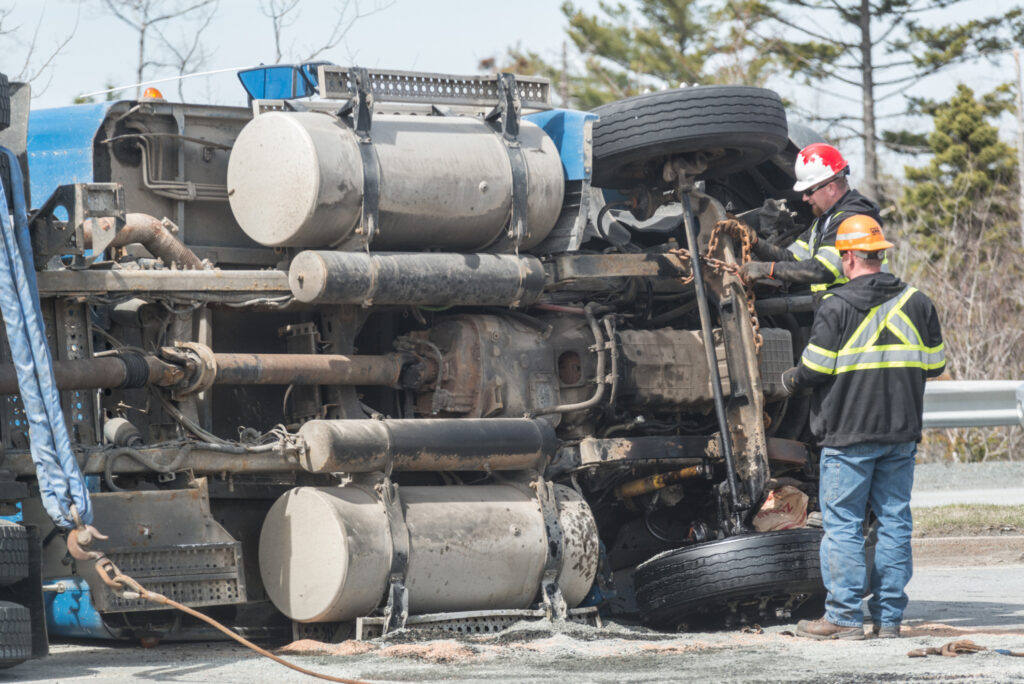
“Is the glass installer supposed to be handling that, or is the body shop supposed to be handling that?” he asks, referring to the camera’s inspection and installation. “Somebody’s got to do it.”
It was just one example that speakers presented during an online presentation for the American Trucking Associations’ Technology and Maintenance Council (TMC).
Traditional paint, body filler, and vehicle graphics could obscure side sensors used to trigger blind spot warnings, while radar sensors might be misaligned and aimed toward traffic in adjacent lanes, Sterwerf says of collision repairs. To compound matters, aftermarket replacement parts might come with different mounting holes for system components.
“If you change the location of that sensor even a quarter of an inch, you can cause that truck to brake erratically,” he warns.
Jim Kolea, president of PennFleet Corporation, refers to another challenge in the form of welding equipment, which can damage a truck’s electronic control modules if grounding clamps and wires are not properly located.
‘Conjunctive damage’
Service providers should also be looking well beyond a point of impact when determining exactly what to repair.
“Look for conjunctive damage,” Kolea says. “There’s so many ways that those G forces will completely change a vehicle.”
It doesn’t begin and end with sensors. Another example can involve aftertreatment systems mounted far behind a crumpled front end.
“That metal is getting heat treated over time and some of the parts get brittle,” Sterwerf explains. Ceramic filters can crack; pipes can shift and begin to leak. The damage might only be apparent after pressure checks and smoke tests.
“Body shops should be looking for this,” he says. “Why should the fleet pay for that aftertreatment system down the road when it was really attributable to someone else who caused the accident?”
Modern material needs
The latest generation of materials used to make the cabs themselves will also respond to forces in unique ways.
The sealers applied in a “massive quantity” when producing floors, back walls, and side walls help to insulate against noise, offers John Spoto, 3M national heavy duty truck commercial fleet manager. But they can also be damaged when exposed to heat.
It isn’t the only way that additional damage could be hiding from view.
Materials selected in the name of lightweighting a vehicle might form internal cracks, Sterwerf says, offering the example of a simple hit on the front axle. “Just because there’s not a crack on the surface doesn’t mean there couldn’t be internal fissures on that casting.”
It’s why he stresses the value of dye penetrant tests, and the 3D measurement systems that can spot the bends not easily identified with the naked eye.
Shops that collect every possible detail about a collision will be better equipped to identify exactly where to focus their attention.
It’s a process that can help to keep repaired trucks off the road until they’re fully ready for service, too. Sterwerf, for example, has seen engines burn up after body repairs were completed because they were left to run too long after a rollover.
There are even repairs that should be delayed until critical details are collected.
“Sometimes that truck needs to be cordoned off and protected,” Sterwerf says, referring to the need to preserve evidence.
Legal implications
It isn’t the only legal issue to consider. If advanced driver assistance systems are compromised during a repair, there could be legal implications when lawyers chase down those who are responsible for future collisions.
“Ultimately the driver and the fleet tend to be on the front end of this, but they’re starting to bring in the repairers,” Sterwerf explains.
Repair teams can also introduce future challenges of another sort if they cut literal or figurative corners. Cutting the right angle on a side panel could sacrifice cab integrity, he says as an example. “The customer and driver will never know that safety structure is gone.”
Specific fasteners are also used to support designs that allow engines to drop below the cab during a collision. Attaching stronger Huck fasteners in the wrong position could affect how well that design works.
And even though a fastener appears to fit, a different material could introduce an unwanted source of galvanic corrosion. Even worse, holes might be enlarged and rivets pushed beyond their design limits.
“Just because the rivet breaks doesn’t mean it’s correct,” Spoto says of the installation.
“The manufacturer is doing everything they can to torque bolts to specification,” he adds. Work like that can easily be undone by a technician who applies too much force with an air wrench, overstretching bolts as if they were Stretch Armstrong action figures.
Alternative fuels
Alternative fuel systems and battery electric vehicles add yet another layer to modern collision repairs. Those working on natural gas vehicles need to ensure shops have the required air circulation before hauling equipment indoors, Kolea notes.
“A body shop is considered a hot shop because we grind and weld,” he says, referring to the need to ensure natural gas tanks are defueled. “The lines and the joints could be compromised and just short of bursting.”
“We can’t ignore all the electrification that’s going on in trucks,” Sterwerf adds, noting how batteries could be damaged by the heat in a paint booth.
The equipment evolves. Collision repair techniques need to evolve with it.
Have your say
This is a moderated forum. Comments will no longer be published unless they are accompanied by a first and last name and a verifiable email address. (Today's Trucking will not publish or share the email address.) Profane language and content deemed to be libelous, racist, or threatening in nature will not be published under any circumstances.
Great Americans!
John great article